This is a Website Demo of the exact site we install for you
Ultimate Guide to Injection Molding: The Right Partner for Your Needs
In the manufacturing world, the term injection molding refers to the process used to create everything from automotive parts to plastic containers and many other everyday items. Injection molding allows businesses to manufacture large volumes of high-quality, economical, and accurate components, ranging from automotive parts to medical devices and consumer goods. According to the research, the success of an injection molding project begins with a successful injection molding company selection. Whether you're a fledgling startup attempting to develop a new product, or an established business aiming to streamline your production, the injection molding company you choose is crucial.
Material Preparation
Raw material, usually plastic pellets, is fed into a heated barrel where it melts.
Injection
The molten material is injected under high pressure into a mold cavity.
Cooling
The material cools and solidifies inside the mold, taking its shape.
Ejection
The finished part is ejected from the mold.
Repeat
The process is repeated for mass production.
Injection molding is widely used because it allows for high precision, repeatability, low production cost, and efficiency in producing complex and detailed parts. It is commonly used in industries such as automotive, medical, consumer goods, and packaging and is ideal for quantities of 1,000 plus. Injection molding requires that a metal mold be made which can take up to 2 months to make. The one-time cost for a mold varies considerably depending upon the size and complexity of the mold.

The Definitive Guide to Injection Molding: Advantages, Applications, and Choosing the Right Partner for Your Project.
In this detailed guide, we’re covering everything you need to know about injection molding, including its advantages, and details on how to select the right partner for your project.
What Is Injection Molding?
Injection molding is a manufacturing process in which molten material—usually thermoplastic or thermosetting polymers—is injected into a mold cavity under high pressure. After being cool and solid, the part is ejected from the mold, and the process starts all over again. This makes it perfect for manufacturing high volumes of identical components with great precision and repeatability.
The Process of Injection Molding: Insights
- Feeding of Material: The raw material, usually in pellet form, is fed into the injection molding machine.
- Heat and Melt: The material is subjected to heat until it reaches a molten state.
- Inject: The molten material is injected into a mold cavity at high pressure.
- Cooling: The material hardens and cools while inside the mold.
- Ejection: The completed part is ejected from the mold.
Benefits of Injection Molding
Injection molding offers many advantages for businesses looking for dependable and scalable manufacturing solutions:
- High Efficiency: The process is highly efficient for mass production once the initial mold is produced.
- Cost-Effectiveness: The more you produce, the lower the cost per unit goes down.
- Design Versatility: Enables intricate geometries and complex designs to be created with high precision.
- Material Versatility: Plastics, rubber, and even metal can be used.
- Durability and Strength: Injection-molded components are typically much stronger than those made with other processes.
- Uniformity: All produced parts are identical.
Uses of Injection Molding
Injection molding is applicable in various industries:
1. Automotive
- Dashboards, bumpers, and interior components
- Lightweight yet durable components for fuel efficiency
2. Medical
- Surgical tools and medical devices
- Sterile, single-use products
3. Consumer Goods
- Electronic enclosures, toys, and kitchen products
- High-throughput part with aesthetic components
4. Industrial
- Custom tooling and gears & enclosures
- Precision machined parts (e.g. for machinery)
5. Aerospace
- Lightweight components for aircraft
- High-strength parts for extreme applications
Your Guide to Selecting the Right Injection Molding Company
Considering who you use for injection molding can determine a theater for your project's overall success. The most important to keep in mind are:
1. Experience and Expertise
Find a company that has extensive experience in your industry and a track record of successful projects. Seek certifications and responsiveness with the industry standards.
2. Possible Subheading
Can you rely on this company for state-of-the-art machinery with expertise in your material and design needs? Find out about their production capacity and turnaround times.
3. Design Assistance
A good partner should provide design help and prototyping help to improve the products prior to mass production. Inquire if they offer:
- CAD design assistance
- Rapid prototyping
- Mold flow analysis
4. Quality Assurance
Quality control is crucial when it comes to injection molding. Confirm the company has a strong quality management system (ISO certification, for example) and conducts frequent inspections.
5. Material Selection
A reputable company will support you in choosing the appropriate material for your application, weigh performance, cost, and sustainability.
6. Cost and Pricing
Ask for quotes in detail and beware of hidden fees. Think of the long-term benefits of engaging with an honest partner instead of one that merely underbids you.
7. Customer Service
Opt for a partner that communicates well, is responsive, and offers post-production support.
The Injection Molding Process — Step by Step
Step 1: Concept & Design
- Determine the product’s requirements and function.
- Work with engineers to develop a 3D CAD model. Step 2: Prototype Development Create prototypes using 3D printing or low-volume molding.
- Prototyping and iteration.
Step 3: Moulding Process
- The inner and outer shape of the shoes is created depending upon the design provided using good quality materials like aluminum, steel, etc.
- Run mold flow simulations to optimize performance
Step 4: Production
- Start mass production on automated injection molding machines.
- Check quality throughout the production cycle.
Step 5: Install and Assembly
- Processes secondary operations, like painting, labeling, or assembly.
- Check final goods prior to shipping.
Injection Molding Materials
Thermoplastics
- Polypropylene (PP)
- Acrylonitrile Butadiene Styrene (ABS)
- Polyethylene (PE)
Thermosets
- Epoxy
- Phenolic resins
Elastomers
- Silicone
- Rubber
Specialty Materials
- Glass-filled plastics
- Biodegradable polymers
Current Trends in Injection Molding
- Sustainable Practices: Growing emphasis on eco-friendly materials and processes.
- Automation: Use of robotics for faster, more accurate production.
- 3D Printing: Hybrid processes that integrate 3D printing and injection molding.
- Smart Manufacturing: Internet of Things-approved gadgets for live tracking.
Why Welch Plastics?
Welch Plastics: Experts in Customized Injection Molding Solutions
At Welch Plastics, we offer personalized injection molding solutions that are designed to meet specific needs. Here’s what sets us apart:
- Industry Knowledge: Over [X years] of working with [specific industries].
- Advanced Technology: The latest in machinery for accuracy and ease.
- All-Rounder: We do everything from design to delivery.
- Sustainability: A focus on environmentally friendly practices and materials.
- Relentless Support: Your success is our success.
Contact us for a Quote Today
If you’re ready to take your project to the next level, we’re here to help! Provide the details and give us a call today for a quote or to book an appointment. Let’s discuss how we can make your vision a reality with quality and dependable injection molding services.
Welch Plastics is the exclusive manufacturer for Jose Canseco’s company PX40/40.
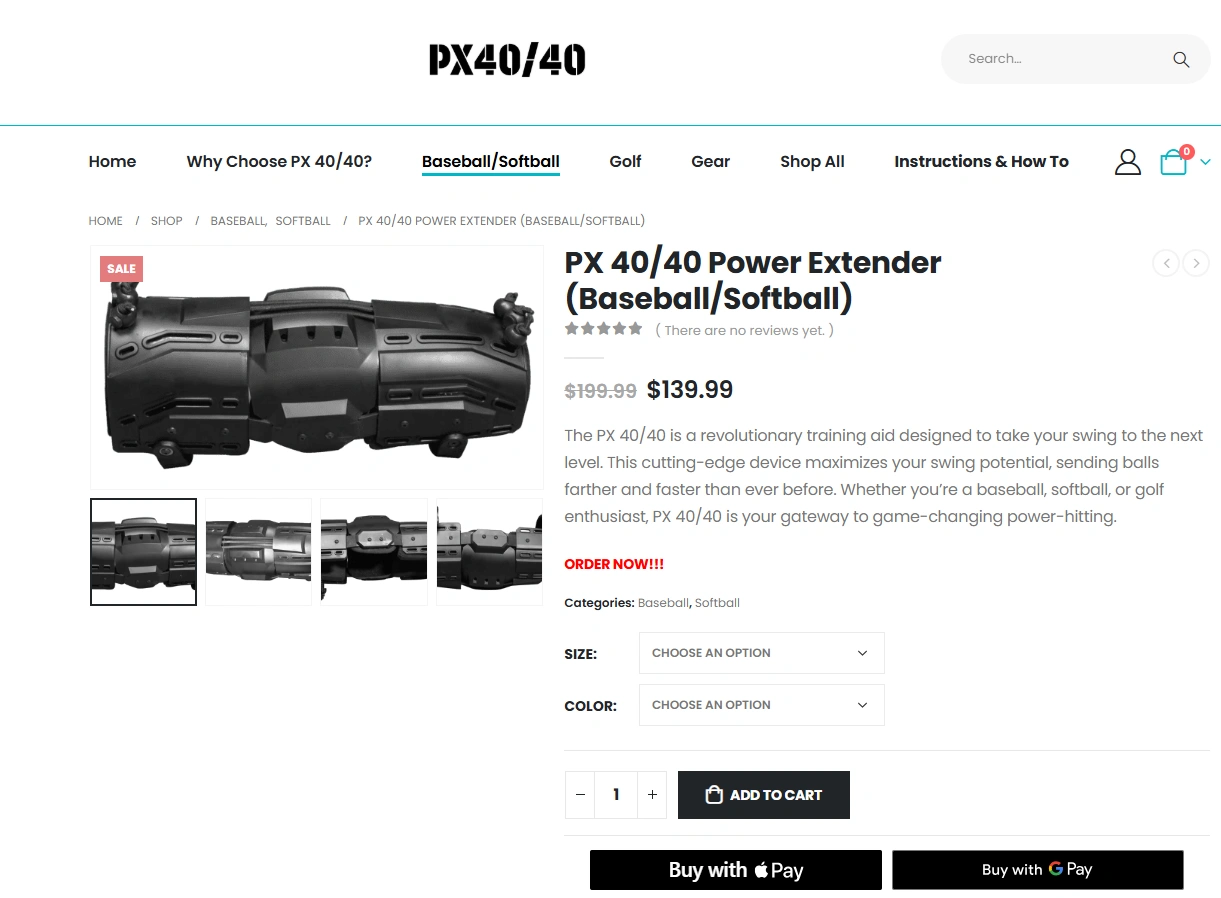
To order PX40/40, please use this link Improve Your Swing with Jose Canseco’s PX 40/40 Power Extender
Check out Jose’s interview about PX40/40
Some of our clients for injection molding services:
PX40/40 Improve Your Swing with Jose Canseco’s PX 40/40 Power Extender
Squirt Boards (website launching summer of 2025)
Museum of Illusion Museum of Illusions
Swift Slice (launching summer of 2025)
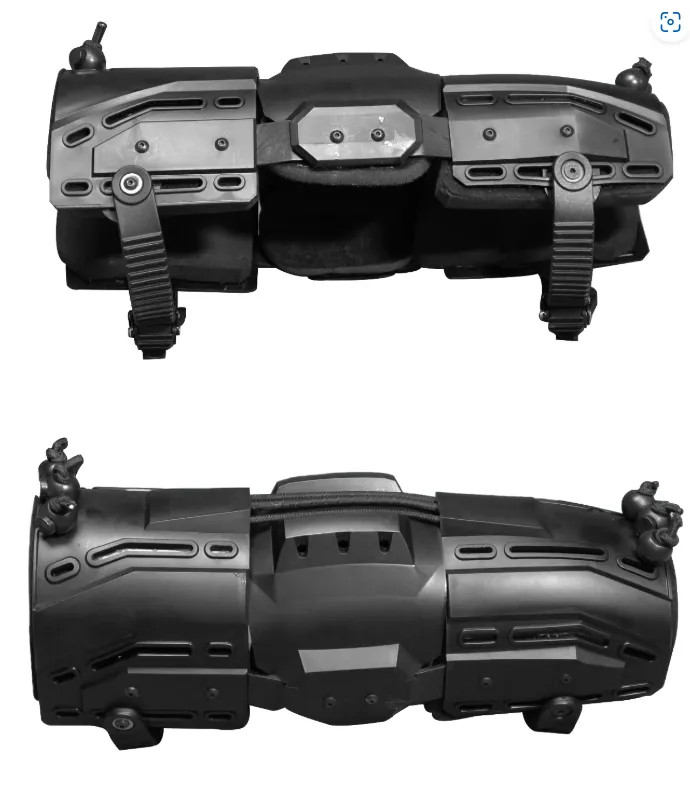
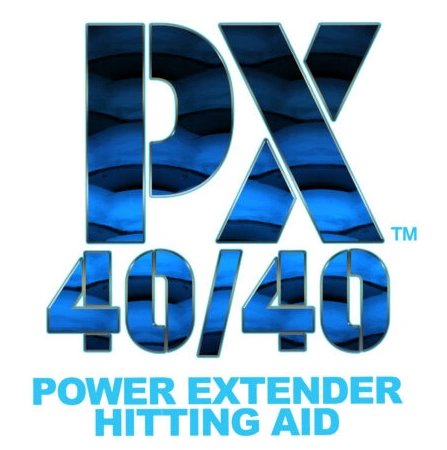
Start A Conversation
Contact us today for a no obligation quote
Where innovation meets durability – We at Welch Plastics continuously offer high-quality, precision plastic fabrication to transform your ideas into reality. Reach out to see what we can create for you.

Since 2000
Welch Plastics
Where innovation meets durability – We at Welch Plastics continuously offer high-quality, precision plastic fabrication to transform your ideas into reality.